Unsere Fabrik
McConnel Power Arms werden in der Produktionsstätte des Unternehmens in Ludlow, Shropshire, präzise gefertigt, wo die Maschinen entworfen, gebaut und getestet werden.
Die überwiegende Mehrheit der Komponenten wird im eigenen Haus hergestellt und jede einzelne Maschine wird einem strengen Testprogramm unterzogen, bevor sie an Kunden ausgeliefert wird.
So verwandelt unser engagiertes Team rohe Stahlbleche in die preisgekrönten Power Arms, die auf der ganzen Welt beliebt sind.
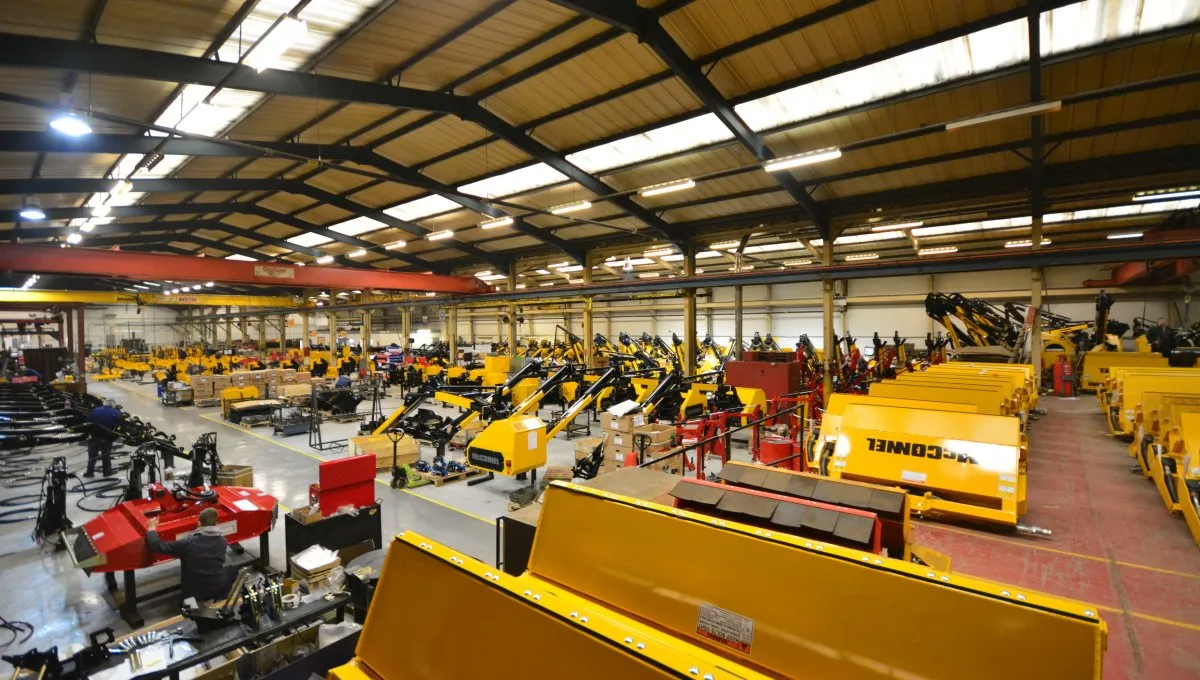
Komponenten
Mehr als 10.000 Bauteile pro Woche werden aus Stahlplatten mit einer Dicke von 1,6 mm bis 65 mm hergestellt. Der Prozess verbraucht bis zu 65 Tonnen Stahl.
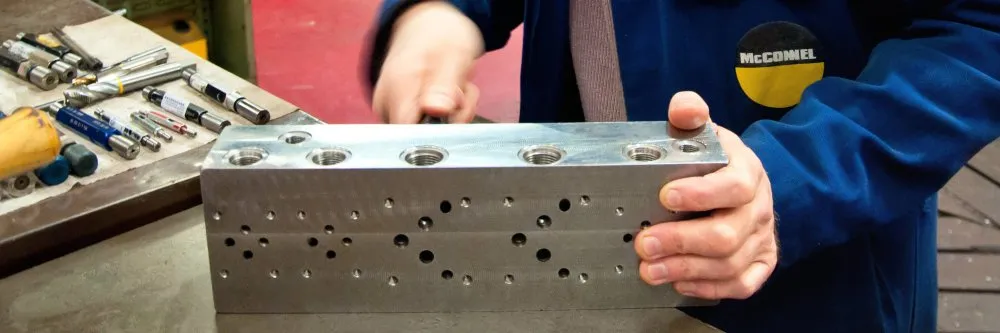